
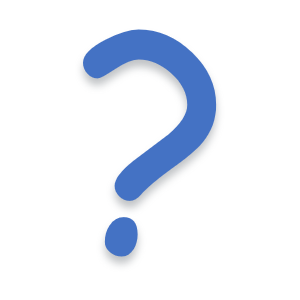
Counter point. Most computer power supplies have a curve to their charging efficiency (somewhere north of 50% load). If your PC is substantially below the peak of that curve, then adding load (the phone) could raise the PSU’s efficiency say from 80 to 85% (I’m making up numbers) which would affect the overall efficiency of the entire PC’s load.
I think your answer is still probably correct, but it’s an interesting nuance to think about.
Side notes: Some PSU’s use gallium, e.g., Corsair ax1600i, though by and large most do not. Also if your in the EU then your working with 220/240v PSU’s which adds more efficiency, but that would apply to the phone charger as well.
Agreed, especially for gaming PC. On laptops and generic PC I think there could be a bigger swing, but also you’d need a USB port capable of pushing 30w which is not a standard feature by any means in a PC/laptop.